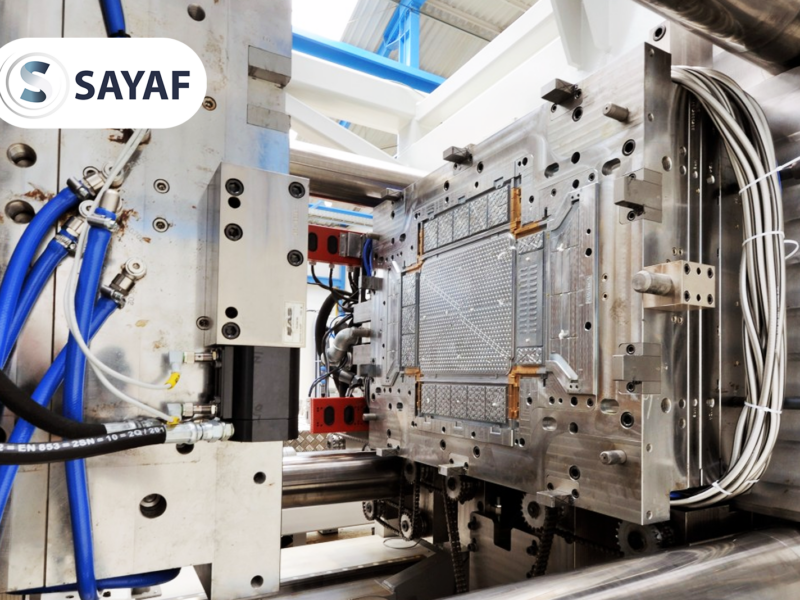
Introduction
The aluminum injection process is one of the most important techniques used in manufacturing high-precision and high-quality metal components. This process relies on injecting molten aluminum into metal molds under high pressure, allowing the production of durable and lightweight parts used in a wide range of industries such as automotive, electronics, and medical devices. In this article, we will discuss in detail how aluminum injection is carried out in factories, its key stages, its most notable advantages, and the modern technologies used in it.
What is Aluminum Injection?
Aluminum injection is a manufacturing process that relies on using metal molds into which molten aluminum is injected under high pressure. This technique is also known as die casting and is widely used to produce complexly designed parts while maintaining high precision in details.
This process relies on specialized machines that melt aluminum and pump it into the mold at high speed, allowing the metal to cool and solidify into its final shape within seconds.
Stages of the Aluminum Injection Process in Factories
The aluminum injection process involves several key stages that ensure the production of high-quality, precision components. Here are the stages in detail:
1. Raw Material Preparation
Production begins with the preparation of raw aluminum, where aluminum alloys are selected based on the required properties of the final product. The aluminum is melted in specialized furnaces reaching temperatures of around 660°C, which is the natural melting point of aluminum.
2. Mold Preparation
The mold is a high-precision metal tool made from heat-resistant materials such as reinforced steel. Before the injection process begins, the mold is cleaned and lubricated to facilitate the flow of molten metal and ensure it does not stick to the mold after solidification.
3. Injection Process
Once the aluminum reaches the required melting point, it is transferred to the injection chamber, where it is pumped under high pressure ranging from 1,500 to 25,000 psi into the metal mold. The high pressure helps fill all parts of the mold quickly and ensures precise details in the final product.
4. Cooling and Solidification
After the injection process, the molten metal begins to cool inside the mold, solidifying and taking the desired shape. The cooling time depends on the size and thickness of the manufactured part but typically takes only a few seconds to minutes.
5. Ejecting the Product from the Mold
Once the aluminum has completely solidified, the mold is opened, and the final product is ejected using mechanical or manual systems. Sometimes, the part may require the removal of excess metal that formed during injection.
6. Finishing and Final Treatment
The produced parts undergo additional finishing processes such as:
- Cleaning and polishing to improve the final appearance
- Removing excess edges to ensure surface smoothness
- Coating or electroplating to protect the product from external factors such as corrosion and moisture
Modern Technologies in Aluminum Injection
With technological advancements, the aluminum injection process has seen significant developments thanks to modern technologies that improve production and efficiency. Some of the most notable technologies include:
1. Smart Control Systems
Many modern factories rely on digital control systems to monitor and adjust temperature, injection speed, and mold pressure, reducing errors and improving product quality.
2. Advanced Molds
Molds are manufactured using precision manufacturing techniques (CNC) and 3D printing, allowing the production of molds with complex details and greater resistance to heat and pressure.
3. Rapid Cooling
Innovative cooling systems have been developed to reduce product cooling time, speeding up production and improving the quality of final parts.
Advantages of Aluminum Injection
The aluminum injection process offers many advantages that make it a preferred choice in manufacturing, including:
- High Precision: Metal molds allow the production of complex parts with precise details without the need for additional manufacturing processes.
- Fast Production: The process offers high production speed, making it ideal for large-scale manufacturing.
- Strength and Durability: Cast aluminum offers high hardness and lightweight properties simultaneously.
- Reduced Waste: Injection helps reduce raw material waste, making it an economical and environmentally friendly option.
Applications of Aluminum Injection in Various Industries
Aluminum injection is used in a wide range of industries, most notably:
- Automotive Sector: Manufacturing engines, lightweight frames, and interior components.
- Medical Industry: Producing precise medical equipment resistant to rust and corrosion.
- Electronics: Manufacturing phone covers and laptop components.
- Household Appliances: Producing frames for devices such as washing machines and refrigerators.
Why Choose Sayaf Group for Aluminum Injection Solutions?
Sayaf Group is one of the leading companies in the field of aluminum injection, offering:
- Modern Technologies: We use the latest die-casting systems to achieve the highest levels of precision and quality.
- Extensive Experience: Our specialized team has extensive experience in mold manufacturing and injection processes.
- Sustainability Standards: We strive to reduce waste and increase production efficiency while adhering to environmental standards.
Conclusion
The aluminum injection process is one of the most efficient and precise manufacturing techniques, used to produce high-quality metal components for a wide range of industries. Thanks to technological advancements, it is now possible to improve production, reduce waste, and increase the precision of final products. If you are looking for professional solutions in aluminum injection, Sayaf Group is the ideal choice to achieve the highest standards of quality and innovation.